Category: Industrial Contracting
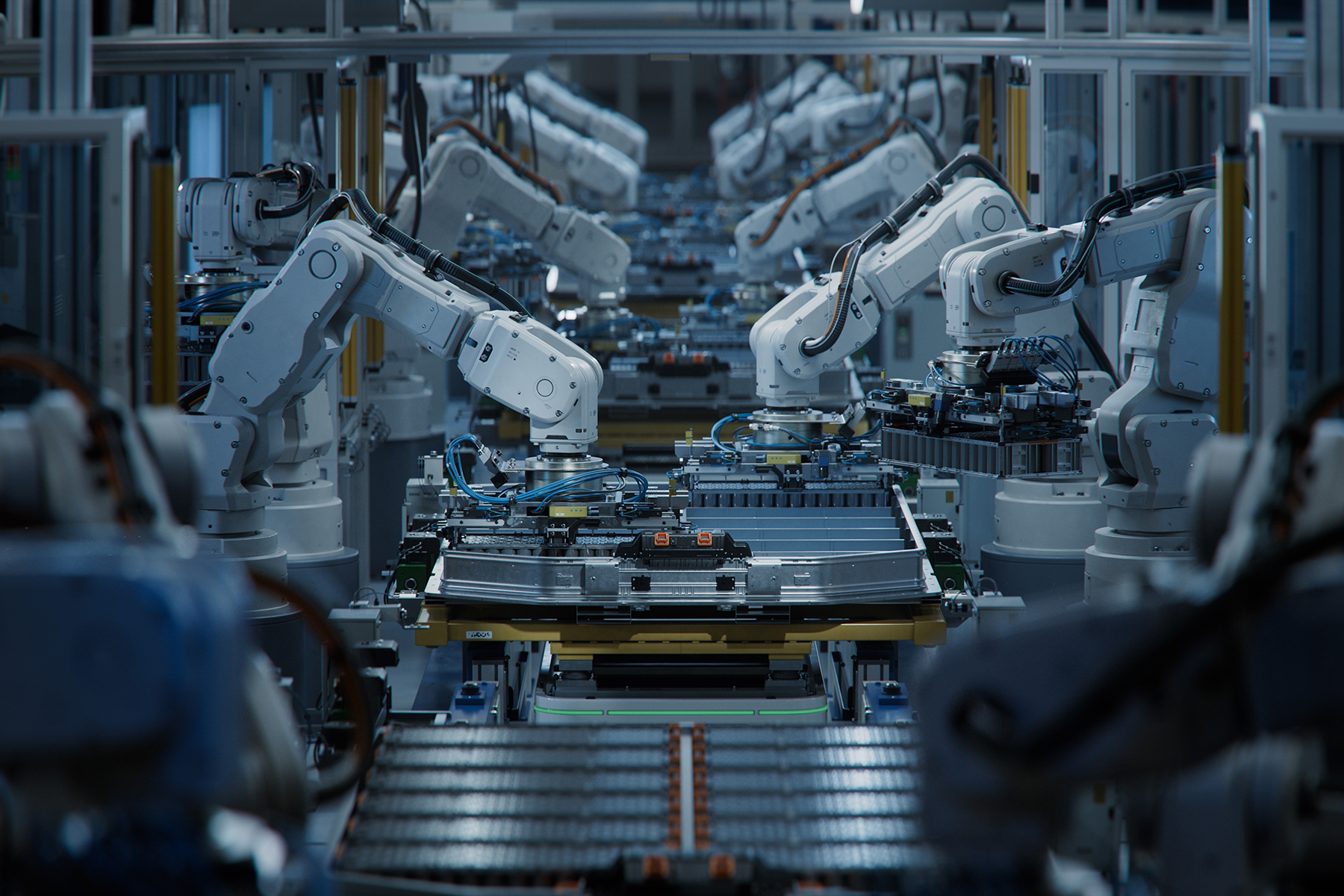
If you walk into a typical manufacturing plant today, you’ll likely come across equipment control systems that are a mix of old and new. Many facilities are still using legacy PLCs and other hardware that was installed decades ago. These systems might be working just fine, but they weren’t designed to communicate with the modern automation tools we see today.
The challenge? Upgrading without bringing your entire plant to a standstill.
The good news is, you don’t have to rip and replace all your legacy systems. At Lee Industrial Contracting, we’ve helped numerous facilities upgrade to automation solutions that integrate seamlessly with legacy equipment.
The key is to approach the project using thorough planning, analysis and a phased approach. Here’s how an experienced industrial contracting company like Lee Contracting helps manufacturers transition smoothly.
Step 1: Define Goals and Priorities
Installing modern equipment shouldn’t just be about having the latest and greatest. You first must ask, “Does this make sense for my business needs?” Here are some questions to consider before modernizing:
• Will modernizing help us meet our goals more efficiently?
• Do we need better access to data or real-time monitoring?
• Will automation help improve safety or compliance?
• Is it cost-effective?
Understanding your goals helps you identify what should be upgraded first so we can build a phased roadmap rather than trying to tackle everything at once.
Step 2: Assess Your Current Systems
Before any plans are made, we first must understand what you’re working with now. An experienced industrial contracting controls team will evaluate everything from the age and condition of your PLCs and HMIs to software compatibility to network infrastructure.
Once the evaluation is complete, we’ll have a better picture of what the project will need. We’ll consider which components can be retained, which will need upgrading and what challenges we might encounter during implementation. We’ll also identify any potential safety issues so we can create plans to avoid them.
Step 3: Design a Phased Integration Plan
Some teams get overly ambitious and think they can perform a complete controls overhaul within a short shutdown window. This is a mistake. Trying to rush the project leaves no time for unexpected issues, thorough testing or proper training – all things that can increase the risk of added downtime.
At Lee Industrial Contracting, we approach modernization with a step-by-step integration plan. This might include:
• Running new wiring and panels in parallel to existing systems
• Upgrading PLCs and software in stages
• Testing new components offline before switching over
• Scheduling cutovers during planned maintenance window
This step-by-step approach breaks up work into manageable phases, allows time to find and fix problems early and enables you to train staff gradually. This way, you avoid surprises and keep your systems running.
Step 4: Execute with Cross-Functional Expertise
Controls integration isn’t just a job for an engineer. Many trades must be brought in to ensure all systems work properly. Electricians, programmers, mechanical specialists and engineers work together and communicate constantly on the project.
This is where working with the team at Lee Industrial Contracting gives you an advantage. Since we have all these trades in-house, we can streamline scheduling and make sure all teams are aligned.
As a self-performing industrial contractor, we can build and install electrical panels, program PLCs and HMIs to interface with legacy equipment and perform testing and validation before go-live.
When all trades are coordinated under one roof, you avoid delays and finger-pointing between multiple industrial contractors.
Step 5: Train and Support Your Team
Even the best technology can fail without proper training. Hands-on training must be conducted to ensure operators and maintenance teams understand the adjustments to their work. This empowers your staff to run and troubleshoot the new controls confidently.
Ongoing support such as remote diagnostics and updates help to keep your operations running smoothly after the upgrade.
The Right Path to Modernization
Integrating automation into your legacy production lines is a smart decision. Partnering with an experienced, self-performing industrial contracting partner helps you bridge the gap between legacy systems and modern automation equipment smoothly. Whether you’re upgrading a single press line or an entire facility, a phased approach reduces risk while you build a smarter, more efficient facility.
Looking to integrate automation into your facility? The self-performing team at Lee Industrial Contracting has the expertise you need. Contact us today.
Subscribe and receive updates via email

In industrial contracting, safety must be placed above all else. Full stop. From complex rigging projects to plant upgrades, the industrial environments where Lee Contracting operates demand the highest level of attention to worker protection and risk management.
Building a strong culture of safety isn’t about doing the bare minimum. It’s about empowering every employee at every level of the company to be an active participant in keeping themselves and their colleagues safe. This commitment is found in each project and process to create an industrial contracting workforce that is accountable and fully understands all aspects of safety.
Setting the Tone Through Leadership
A culture of safety starts at the top, and Lee Contracting’s leadership team goes to great lengths to make sure the team understands safety is a core value. Our leaders prioritize safety in every decision and allocate resources to support it. They hold themselves and others accountable for maintaining the highest standards.
This visible commitment breeds trust across the entire organization and sends a clear message: safety matters here and everyone plays an important role.
Building an Infrastructure of Safety
To ensure our safety efforts are proactive and pervasive, Lee Contracting has built a company-wide infrastructure of safety that supports our industrial contracting services, led by two key groups:
Safety Team
Our Safety Team is made up of experienced professionals skilled in hazard identification and the application of effective mitigation strategies. Many team members hold advanced degrees and are certified OSHA Outreach Trainers for OSHA 10 and 30-hour courses in both General Industry and Construction.
The Safety Team is responsible for identifying potential hazards within every project and conducts thorough risk assessments to recognize safety concerns early and continuously. Based on these findings, Lee Contracting develops and implements comprehensive mitigation strategies to minimize risks and ensure compliance with all safety regulations.
Safety Committee
Separate from our Safety Team, our Safety Committee is made up of employees who volunteer from all levels of the organization and have shown a commitment to supporting and strengthening our safety culture.
Each member holds, at minimum, an OSHA 30-hour certification and serves as an extension of our full-time safety staff, assisting in identifying hazards and implementing corrective actions. As subject matter experts in their respective fields, they provide valuable insight into specific means, methods and trade-specific techniques. This expertise bolsters our ability to proactively address potential hazards and implement realistic, field-informed solutions.
Safety Scoring and Analysis
Every project is assigned a safety score that guides safety planning and oversight. This scoring system helps ensure that appropriate safety measures are aligned with the specific risks and requirements of each project. Pre-Task Planning (PTP), Job Hazard Analyses (JHA) and onsite visits ensure safety expectations are communicated clearly and followed consistently throughout the entirety of the project.
Empowering Every Employee
Empowering employees to take ownership of safety is key to Lee Contracting’s safety approach. The company provides and supports:
Robust training: All trades personnel complete at least OSHA 10-hour training at the apprentice level and OSHA 30-hour training for field supervisors. Additional trade-specific and role-based training is also provided to reflect the latest best practices and regulatory requirements. Our in-house First Aid and CPR course, certified by the American Red Cross, has received stellar feedback and further equips employees to respond appropriately in emergencies.
Stop Work Authority (SWA): Employees are not just empowered, but encouraged, to stop work if a potential hazard is identified. Team members who exercise SWA are recognized, and the company issues rewards and incentives like safety scratch-off tickets, raffle entries, and nominations for the Safety Championship awards.
This commitment to empowering our workforce is one of the many reasons clients trust Lee as their industrial contractor on complex, high-risk projects.
Award-Winning Safety
Lee Contracting’s commitment to safety has earned significant industry recognition, including:
- 2025 Associated Builders and Contractors STEP Program Level Platinum for outstanding Safety Practices
- 2024 Associated Builders and Contractors STEP Program Level Gold for outstanding Safety Practices
- 2023 Associated Builders and Contractors STEP Program Level Silver for outstanding Safety Practices
- 2023 Construction Association of MI Honorable Mention for outstanding Safety Practices
- 2020 Construction Association of MI Honorable Mention for outstanding Safety Practices
- 2019 Construction Association of MI Honorable Mention for outstanding Safety Practices
- 2018 Construction Association of MI Bronze Award for outstanding Safety Practices
- 2018 General Motors Supplier of the Year
At Lee Industrial Contracting, building a culture of safety is about more than checking boxes. It’s about empowering our people to always put safety first. By investing in extensive training and encouraging proactive participation from every team member, we create a workforce where safety is not just a core value, but a source of pride.
Do you have an upcoming industrial project and need a team that puts safety first? Contact us today to see how we can help.
Subscribe and receive updates via email

The future of industrial automation is already underway, and it’s changing the nature of manufacturing operations and facility upgrades. No matter if you’re planning a major equipment installation or building a new line, automation is becoming an essential part of the equation you shouldn’t ignore.
Forward-thinking manufacturers are working with industrial contracting companies that understand how to integrate automation into each phase of a project – from design and pre-planning to construction and long-term efficiency. Here are five automation trends to keep an eye on.
1. Smart Sensors and IIoT
The Industrial Internet of Things (IIoT) connects machines and sensors to a centralized network, helping manufacturers monitor everything from equipment performance to energy usage in real time. Smart sensors embedded into machines and systems collect data on temperature, vibration, flow and energy usage.
This translates to receiving warning alerts before machines fail, smarter energy use and improved quality control. IIoT data can be used to help guide predictive maintenance, reduce downtime and optimize processes – all of which can be integrated during a facility upgrade or new build with the help of a savvy industrial contracting partner.
2. Robotics
Robotic automation has evolved beyond traditional assembly lines. Today, collaborative robots (called “cobots”) and autonomous mobile robots (AMRs) are not replacing workers, but working alongside them to reduce staff exposure to hazardous environments while keeping production moving smoothly.
An industrial contracting partner that understands robotics can help you incorporate solutions like automated welding, robotic palletizing or material transport systems to improve throughput and workplace safety.
3. Controls Automation
If robots are the “hands” and sensors are the “eyes,” then controls automation is the “brain” that ties it all together.
Modern control systems, including PLCs (Programmable Logic Controllers), RFID tracking and HMI dashboards, orchestrate your equipment’s behavior in real-time. Whether you’re operating a stamping press, conveyor system or hydroforming unit, automation logic ensures everything runs precisely and in sync.
An experienced industrial contracting company can design, build and program these systems to not only work with your existing setup but also scale with your future growth.
4. BIM and Digital Twin Planning Tools
Advanced planning tools like Building Information Modeling (BIM) and digital twins let manufacturers visualize their facilities in detail before any concrete is poured or equipment is installed.
These technologies allow you and your industrial contracting team to identify potential layout conflicts, improve spatial planning and simulate workflows in advance of the project. With digital twins, you can even monitor real-time conditions after construction is complete. The result? Smarter, smoother projects and fewer surprises.
5. Automation for Sustainability
Sustainability is not just a trend. It’s an essential foundation of any modern industrial facility. And even better, it can dramatically improve your bottom line. Automation is playing a major role in helping manufacturers reduce waste, save energy and meet environmental goals.
Industrial contracting services can now integrate smart systems that monitor HVAC usage, optimize lighting and regulate compressed air systems to avoid waste. Modular construction methods also reduce material use and allow for faster, cleaner installations. “Green” automation can help deliver ROI while meeting environmental standards.
6. AI and Predictive Analytics
You didn’t think we’d write an article about the future of industrial automation without including AI, did you? Unsurprisingly, artificial intelligence (AI) is playing a role manufacturing environments. In particular, AI provides predictive analytics that can help you schedule maintenance before a breakdown happens, optimize production schedules and even identify which systems should be upgraded first.
When your industrial contracting company understands how to pair AI-driven insights with physical system design, you gain a powerful competitive edge. It’s about using your facility’s data to get ahead of problems, not just react to them.
Incorporating Automation Into Your Facility
Working with an industrial contracting company that understands automation – from design to execution – is key. With fully in-house teams and expertise in automation for mechanical, electrical, fabrication, rigging and controls, Lee Contracting delivers fully integrated industrial contracting services designed for modern manufacturing that keep you well-positioned for the future.
Ready to future-proof your facility? Talk to us about how automation can power your plant’s performance.
Subscribe and receive updates via email

Here’s a hard truth: industrial projects rarely go exactly as planned – especially when they’re complex. Whether it’s unexpected structural challenges, space constraints, or tight deadlines, technical expertise and problem-solving are of course essential, but one thing that’s often overlooked is the power of collaboration.
In complex industrial environments, teams must work together seamlessly – from the pre-construction phase through completion – to ensure projects are successful and stay on track.
But not all collaboration is created equal. When multiple industrial contractors and subcontractors are involved, miscommunication, delays, and inefficiencies can cause delays and overcomplicate issues. That’s why working with an integrated, self-performing industrial contracting team – one that can tackle every phase of a project in-house – can make a world of difference.
The Power of True Collaboration
Effective problem-solving in industrial environments depends on several factors:
Cross-Disciplinary Expertise
Complex projects need input from multiple disciplines, such as rigging, electrical, mechanical, fabrication, and more. In traditional setups, each contractor focuses only on their piece of the puzzle, which often leads to coordination gaps with other industrial contractors and the facility.
A fully in-house, integrated team works together from start to finish and makes sure nothing falls through the cracks.
Adaptability Amid Challenges
When it comes to complex industrial projects, unexpected hurdles like structural issues, equipment failures, or shifts in timeline demand quick attention and adjustment. When everything is handled by a self-performing team, problems can be solved in real time without waiting on outside vendors.
Collaboration That Drives Success
While custom industrial projects require a high level of technical know-how, a problem-solving mindset and a collaborative approach are must-haves as well.
When engineers, tradespeople, and project managers communicate well and goals are aligned, projects and budgets stay on track. When industrial contractors bring a collaborative approach, businesses feel more confident knowing they have a reliable partner to help them navigate any obstacles.
A Case Study of Collaborative Problem-Solving
When Wico Metal Products needed to install new 26-foot stamping presses in their facility, they ran into a major obstacle: the building’s roof wasn’t high enough. The only way to make the presses fit was to raise the roof – by 12 feet. On top of that, winter was approaching, and they had less than five months to complete the job.
From the start, Lee Industrial Contracting worked closely with Wico, ensuring they fully understood the process and how each step would impact their operations. Lee explained the structural requirements, timeline, and necessary modifications, while Wico provided their expectations, concerns, and operational constraints.
This back-and-forth collaboration allowed both teams to refine the approach and agree on the best path forward.
Together, we developed a plan that addressed multiple project needs at once:
- Structural modifications: Raising the roof while maintaining the building’s structural integrity.
- Space optimization: Demolishing outdated office space and enclosing a courtyard to maximize manufacturing space.
- Seamless project management: Handling electrical, plumbing, and mechanical adjustments in parallel with construction.
With everything under one roof, we were able to streamline collaboration directly with the client and accelerate execution, avoiding the communication and scheduling delays that typically come from juggling multiple contractors.
By keeping Wico informed at every stage and adjusting plans as needed, Lee ensured the project stayed on track, met the tight deadline, and delivered a better-optimized facility.
Read the full case study here >
Collaboration Starts During Pre-Construction
One of the most effective ways to ensure collaboration is to bring in industrial contractors early in the process during pre-construction. Involving contractors at this stage allows for value engineering, where we can identify innovative solutions to save costs and streamline execution.
Plus, contractors can fast-track schedules when delays arise due to sector volatility or unexpected challenges. Early involvement helps identify potential obstacles and creates a smoother path to project completion.
Lee Industrial Contracting embraces and adopts a truly collaborative approach in every project. If you’re thinking about starting an industrial project, contact us today to begin the collaboration process and ensure a smoother project – at the lowest cost possible.
Subscribe and receive updates via email
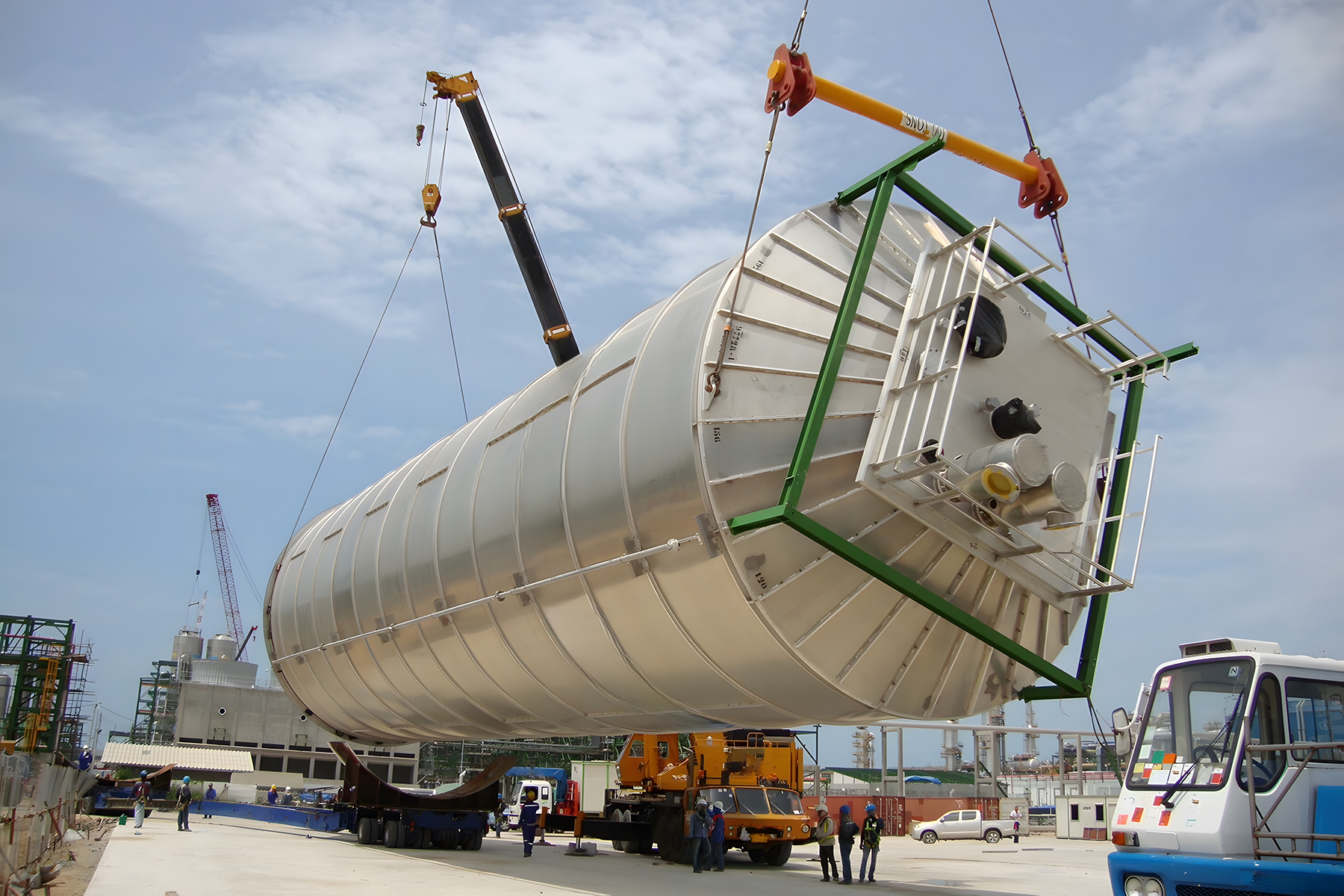
It was supposed to be a simple move – relocating a large piece of equipment to another part of the facility was projected to take just a few days. But once the project started, problems began piling up.
The industrial rigging contractor finished their part, but the electrical team wasn’t scheduled for another three days. Then, a crucial support bracket turned out to be the wrong size and the company had to wait a full week for an outside industrial fabricator to make a replacement.
What was meant to be a short disruption stretched into nearly a month of downtime, putting production behind schedule and causing frustration at every level of the business.
If this scenario sounds familiar, you’re not alone. This type of situation plays out all too often in industrial relocations, and the main issue is this: too many industrial contractors and too many moving parts, all operating on their own timelines.
The key to avoiding these delays? A single-source, turn-key approach.
The Power of One: An In-House, Turn-Key Solution
When it comes to industrial projects, coordinating multiple vendors and the headaches it brings can drag out timelines and lead to more downtime. But if you work with an industrial contractor that can handle every aspect of the project in-house without needing to subcontract, like Lee Contracting, you can dramatically shrink timelines and downtime.
So instead of juggling separate contractors for rigging, electrical, mechanical, and fabrication, you get a fully integrated team that works together from start to finish. This means:
- One project manager overseeing the entire process.
- No delays waiting on subcontractors.
- The ability to adapt in real-time to challenges.
Lee Contracting’s “Power of One” approach ensures that machinery relocations happen as efficiently as possible, minimizing downtime so you can get back to normal operations quickly.
How Lee Contracting Gets the Job Done Faster
When it comes to equipment transfers, the ability to move quickly is everything. Downtime means lost revenue, and every delay adds up. That’s why in-house teams and resources make a critical difference.
Here are just a few advantages that The Power of One brings:
- Rigging Without the Wait: Because Lee has its own heavy-lift equipment and employs full-time rigging specialists, projects don’t get stalled waiting on availability from an outside contractor. If something needs to be moved, we can deploy rigging teams immediately.
- On-the-Spot Fabrication: Unexpected issues during a project often turn up, including missing or incorrect parts. Instead of waiting days or weeks for an external fabricator to deliver a solution, an in-house fabrication team can custom-make the needed part on demand, keeping the project moving.
- Immediate Installation: Because the electrical and mechanical teams are part of the same company as the rigging crew, installation can begin as soon as relocation is complete with no lag time between phases.
This integrated approach means that what could take weeks with multiple contractors can often be completed in days, saving your company time and money.
How a Turn-Key Approach Contributes to Long-Term Success
A turn-key approach delivers benefits far beyond just the one move. When you work with a team that handles everything in-house, you’re not just getting a one-time solution, you’re building a partnership.
This means the next time you need to expand or reconfigure your plant, you won’t have to start from scratch. You’ll have a team that already understands your facility, your equipment, and your operational goals, so every future project goes faster and smoother.
Equipment relocation doesn’t have to mean weeks of downtime. By tapping into Lee Contracting’s Power of One, you can complete a major equipment relocation as quickly as possible so you can avoid extended downtime and keep production on track.
Need to relocate industrial equipment? Request a quote from our team today.
Subscribe and receive updates via email
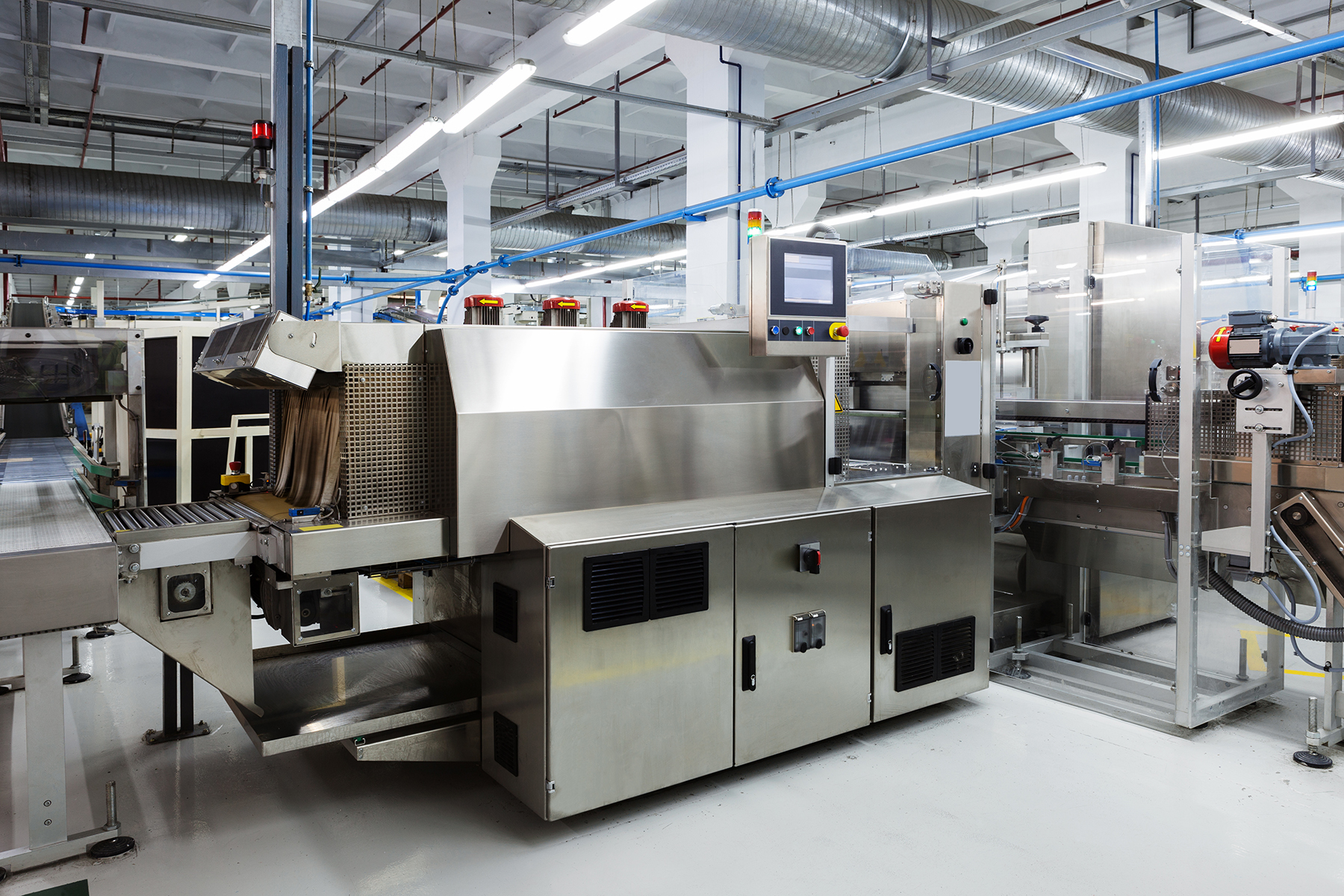
Relocating industrial machinery isn’t just about moving heavy equipment from point A to point B. It’s a highly technical process that demands a strong level of both precision and expertise. Indeed there is a science to it – engineering, technology and mathematics play a huge role. But there’s also the art – pulled off by masters of the craft who find creative solutions to tough challenges and execute complex moves with ingenuity.
Let’s go over each component to understand exactly what goes into a successful industrial machinery relocation.
The Science: Precision Engineering and the Right Equipment
Moving large, heavy-duty industrial machinery demands exacting precision. The weight, balance, and structural considerations of every piece requires detailed engineering analysis before lifting begins. That’s where advanced technology and specialized equipment make all the difference.
3D computer modeling helps map out complex moves and can evaluate clearance restrictions, structural limitations and any potential hazards. This level of planning enables us to simulate every move so we can virtually experience any possible issues that may arise and plan the execution of our industrial rigging services accurately.
Something that’s often overlooked is the expertise of the operators running the equipment. We’re talking about 800-ton gantry systems, 200,000-pound forklifts and modular transporters, so proper training and experience using this equipment is key. That’s why it’s essential to choose an industrial contractor that owns their own equipment, because their team has an advanced level of precision and familiarity that improves safety and efficiency. Operators who work with the same machines daily understand their capabilities and limitations inside and out, leading to smoother, faster relocations.
The Art: Creative Solutions for Complex Moves
Not every machinery move follows a straightforward path – we know from experience that each one is unique. There could be tight spaces, low ceilings or extra-fragile infrastructure that may need innovative problem-solving.
Industrial contractors often must engineer custom solutions, such as temporary support structures or specialized lifting fixtures, to navigate difficult environments without unnecessary disassembly. In other cases, disassembling the equipment might be the better choice. It takes an experienced professional to know the difference.
For example, some moves require lifting equipment through rooftops, which typically means extensive structural modifications. However, roof-raising processes can eliminate the need for costly demolition, allowing for a more efficient move with minimal disruption.
This kind of ingenuity is what sets apart true experts in industrial rigging services from standard heavy equipment movers.
How to Ensure Flawless Execution
Even with thorough planning and cutting-edge technology, at the end of the day, it all comes down to execution. And a successful machinery relocation project means having the right team, equipment and project management in place.
An industrial rigging services provider who offers 100% turn-key, in-house solutions gives you a major advantage because it eliminates the need to coordinate multiple vendors and rent expensive equipment. When one team manages every phase – from disassembly and transport to reinstallation and alignment – it prevents costly delays and miscommunications. A dedicated project manager ensures that every detail is handled professionally, keeping operations on schedule and within budget.
Industrial machinery relocation is a high-stakes operation that demands both technical expertise and creative problem-solving. Choosing the right industrial rigging services partner means working with a team that not only understands the science behind safe equipment handling – but also has the experience and problem-solving acumen to navigate complex moves.
Lee Contracting has the in-house team and equipment needed to handle even the most complex industrial machinery relocations. Contact us to learn more about how we can help with your move.
Subscribe and receive updates via email
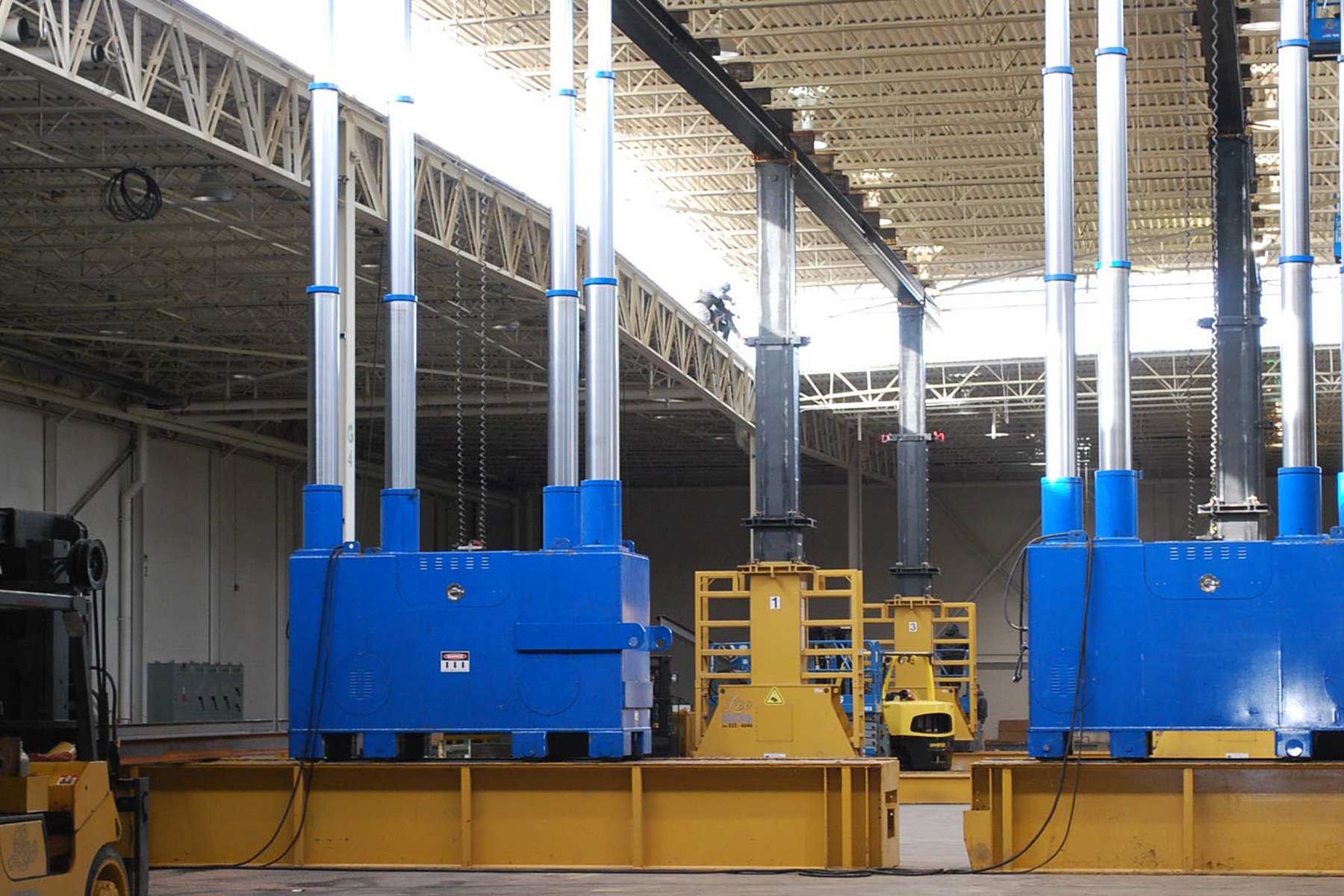
As your business and industries evolve, renovating your industrial facility will be necessary at some point. This is actually a significant milestone – it signals that your company has stood the test of time and is ready for improvements that boost efficiency, safety and productivity.
While a renovation is an exciting step toward improving and optimizing your facility, it does come with its challenges while going through it. In particular, how do you make major changes to your space without affecting day-to-day operations? Even minor disruptions can lead to costly downtime, so strategic planning is essential.
We’ve put together a guide to industrial facility renovation planning so you can keep production running smoothly while making necessary upgrades. By following this guide – and working with an experienced industrial contractor – you can minimize disruptions while ensuring a successful renovation project.
1. Assess the Scope and Impact
As with nearly any industrial project, proper planning is an essential first step that can make a huge difference to ensure the entire project goes smoothly. Before starting any renovation, you must first evaluate exactly how the project will affect daily operations.
Before beginning your renovation, be sure to conduct a thorough site assessment to identify the areas that need work and how construction might interfere with your systems. What are the high-priority zones that must remain operational? What might pose a potential risk – such as disruptions to power, HVAC, or safety systems?
A detailed impact analysis helps create a renovation plan that allows you to anticipate and prepare for any hiccups, helping to keep downtime to a minimum.
2. Go with a Phased Approach
One of the best ways to maintain operations during renovations is by breaking the project into manageable phases. Prioritize upgrades that have the least impact on workflow and schedule major work during off-peak hours or planned downtime.
For example, if you know that spring is your busy season but summer is typically slower, you can schedule less disruptive renovation work during peak times and save the more demanding upgrades for when you know production will be slow.
A well-structured timeline goes a long way in making sure no critical areas are compromised so your team can continue production while renovations move forward.
3. Consider Temporary Solutions
To maintain productivity, consider implementing temporary solutions that allow your industrial facility to function while work is underway.
This could include setting up temporary workspaces, rerouting operations or using modular construction to minimize on-site disruptions. Prefabricated components can also help speed up installation, reducing the time needed for on-site work.
A skilled industrial contracting partner should be able to construct these areas so your team can continue performing their core jobs.
4. Leverage Technology
Incorporating technology into the planning process can help anticipate challenges and streamline renovations. Creating digital twins and 3D modeling helps facility managers and industrial contractors visualize the entire renovation process before it begins, so they can identify potential conflicts in advance.
By simulating real-world conditions in a virtual environment, digital twins and 3D models allow teams to test different renovation scenarios, optimize workflows and foresee potential bottlenecks. Additionally, these tools can be used to map out temporary workarounds, such as rerouting foot traffic or repositioning equipment, to maintain productivity throughout the project.
5. Maintain Safety and Compliance Throughout
Nothing derails operations like an accident or injury. During any renovation, safety must be a top priority, especially when new work is happening alongside rote operations.
Clear safety protocols should be drawn up and implemented to protect both employees and contractors. Compliance with OSHA and industry regulations is essential, and regular safety inspections should be conducted to ensure a secure work environment.
Be sure to educate and communicate with your employees to make sure they understand potential hazards and how to deploy the appropriate safety measures.
6. Select the Right Industrial Contracting Partner
One of the most important decisions you can make is choosing an industrial contractor with experience conducting renovations while your operations continue. Look for a partner with experience working in active industrial environments and offers a full range of services – including design, engineering, fabrication, rigging, electrical and mechanical contracting.
Pro tip: Be sure to involve your industrial contracting partner as early as possible in the process. An experienced partner has performed facility renovations numerous times and can propose creative solutions you may not have considered.
A contractor who has fully in-house teams and doesn’t rely on subcontractors provides better control of project timelines, quality and communication. A strong relationship with an experienced industrial contracting company, like Lee Contracting, ensures that work is completed efficiently with minimal disruption to your operations.
Contact us today to discuss how we can support your next renovation project.
Subscribe and receive updates via email
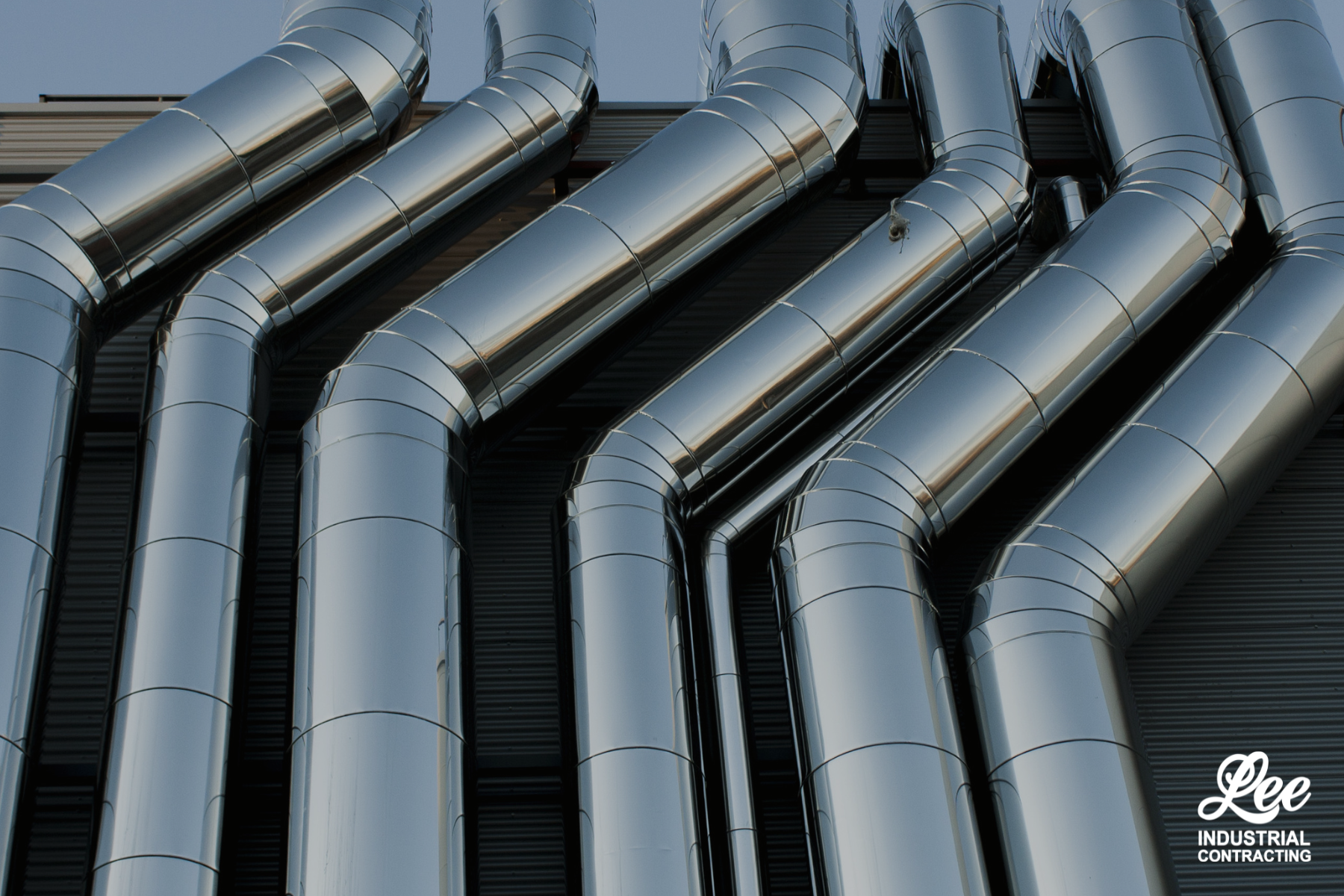
Your industrial facility has a number of moving parts that need to work together in harmony – similar to an orchestra. Each mechanical system plays an important role, from the HVAC providing the right atmosphere to the pipefitting and compressed air systems maintaining the tempo of operations. If one “instrument” fails, the entire symphony risks falling apart.
If you want to keep your facility humming along efficiently, you need more than just a repair service for when things go south. You need an industrial mechanical services partner who understands how to conduct and fine-tune the entire ensemble.
Preventive Maintenance Is the First Step
System failures often stem from issues that could have been avoided with proper planning. When you work with a skilled industrial mechanical contractor, they don’t just respond to breakdowns, they proactively work to prevent them.
Ensure your equipment stays in prime condition by scheduling consistent preventative and predictive maintenance. By conducting regular inspections and applying proactive strategies like contingency plans, you mitigate risk and have a better chance of a quick recovery when unexpected issues do arise.
What to Look for in a Partner
Choosing the right industrial mechanical services partner is more important than you might think, because they are not all the same. The wrong partner could cause further delays, or at worst, result in costly damage to your equipment.
Here are some key questions you should ask a potential partner:
How Much Experience Do They Have?
How well-versed is the contractor in the systems you rely on? Look for a partner with a proven track record of working with facilities like yours. They should have many years of experience working in similar environments and be confident in addressing your questions and concerns.
What Services Do They Offer?
Does the contractor offer end-to-end services – including design, fabrication, installation, and repairs – or are they limited? A full-service partner provides more value by understanding ALL of your systems so issues are diagnosed accurately and addressed appropriately.
Do They Have a Fully In-House Team?
Who will be working on your systems? An in-house team means better control over quality and timelines, while subcontractors can introduce scheduling delays or conflicts that disrupt the process. Be sure to go with a partner who can take ownership of the entire project.
How Responsive Are They?
When an emergency eventually crops up, time is of the essence. It’s frustrating when your industrial mechanical contractor can’t show up when you need them. Ask if they offer 24/7 service and what their average response time is. They should have the capabilities and staff to be able to respond to emergencies quickly to get you up and running again.
Are They Focused on Building a Long-Term Relationship?
A true partnership goes beyond a one-time service call. When an ongoing relationship is built over time, your industrial mechanical services partner gains a deep understanding of your facility’s inner workings and your business needs. This familiarity ensures they know exactly where everything is, can address issues quickly and provide recommendations that make the most sense for you.
At Lee Contracting, we pride ourselves on being more than just a service provider – we’re a trusted partner focused on your success. With a highly experienced in-house team, a full range of industrial contracting capabilities and 24/7 service, we keep your mechanical systems in perfect harmony to ensure each component works together to support the rhythm of your operations.
Partner with Lee Contracting to support your industrial equipment and mechanical systems. Contact us today.
Subscribe and receive updates via email
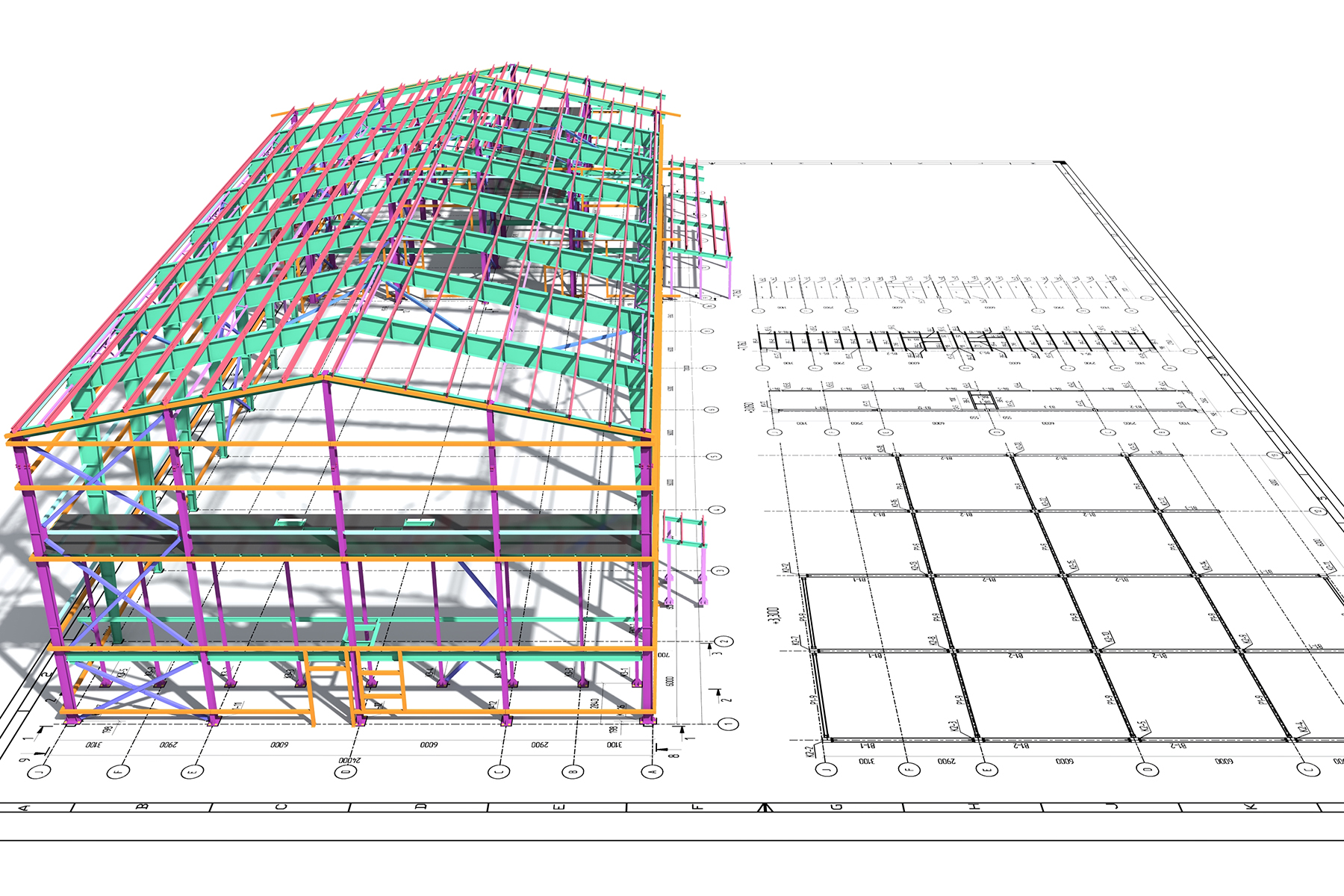
When your manufacturing or industrial business grows, that’s generally considered a good thing. However, “growing pains” are real, and growth isn’t without its own set of challenges. One of the biggest challenges for industrial facilities is limited space for growing operations.
Expanding your facility is exciting, but it isn’t just about adding square footage – it’s about doing so efficiently, cost-effectively and with minimal disruption to production. In today’s environment, innovative tools and technologies are making facility expansion easier and more efficient, and our industrial contracting team is staying ahead of the curve.
Precision Planning in Modern Expansions
When done right, facility expansions start well before construction begins. Planning accurately ensures that every square foot of new or reconfigured space meets operational needs while minimizing waste.
Advanced tools like Building Information Modeling (BIM) software help businesses and industrial contractors visualize, simulate and optimize their designs prior to the physical work. At Lee Industrial Contracting, we’ve embraced this technology by implementing Trimble Tekla Structures into our concrete design and engineering workflows. This powerful BIM software allows us to create highly detailed 3D models that bring clarity to every stage of an expansion project.
By identifying potential challenges early in the design phase, we can avoid costly delays and maximize the use of available space.
Taking BIM Models into the Field
The advantages of BIM software don’t stop at our planning table. One of its most significant benefits is the ability to easily share information with customers, engineers and field crews. Lee Industrial Contracting takes it further by tying the BIM data to robotic layout equipment used in the field. This ensures that designs translate perfectly into real-world execution with incredible accuracy.
For facility expansions, precision matters. Small mistakes can add up to costly delays or unusable space. By leveraging tools like BIM and robotic layout technology, we streamline construction workflows, reduce rework and maintain schedules.
Maximizing Space While Minimizing Waste
Facility expansions require balancing operational needs, speed and cost considerations. BIM tools help reduce material waste by optimizing designs and accelerate the project with ultra-precise advance planning to reduce errors on the job site.
Whether you’re expanding a production line, adding warehouse capacity or upgrading infrastructure, a streamlined approach to design and execution means faster, smarter growth.
A Forward-Thinking Approach to Facility Growth
While BIM software is slowly becoming a fixture in the foundations industry, early adopters have a clear advantage. At Lee Industrial Contracting, embracing tools like advanced BIM software isn’t just about meeting today’s needs, it’s about laying the groundwork for future growth.
Our use of BIM marks an important step toward creating even more capabilities in virtual design and construction. By integrating cutting-edge solutions into our already proven process, we’re continuing to set new standards for precision and efficiency, helping businesses achieve their expansion goals with minimal disruption to operations.
Ready to Expand? Partner with a Team That Innovates
At Lee Industrial Contracting, we believe that innovation drives efficiency. By integrating advanced tools like BIM software and robotic layout technology into our process, we’re redefining what’s possible for facility expansions.
If you’re planning to grow your operations, don’t rely on outdated methods. Partner with an experienced industrial contractor that leverages innovative technology to deliver precision, efficiency and value.
Let’s build the space you need. Contact us today to learn more about how Lee Industrial Contracting can help you grow – without the pains.
Subscribe and receive updates via email
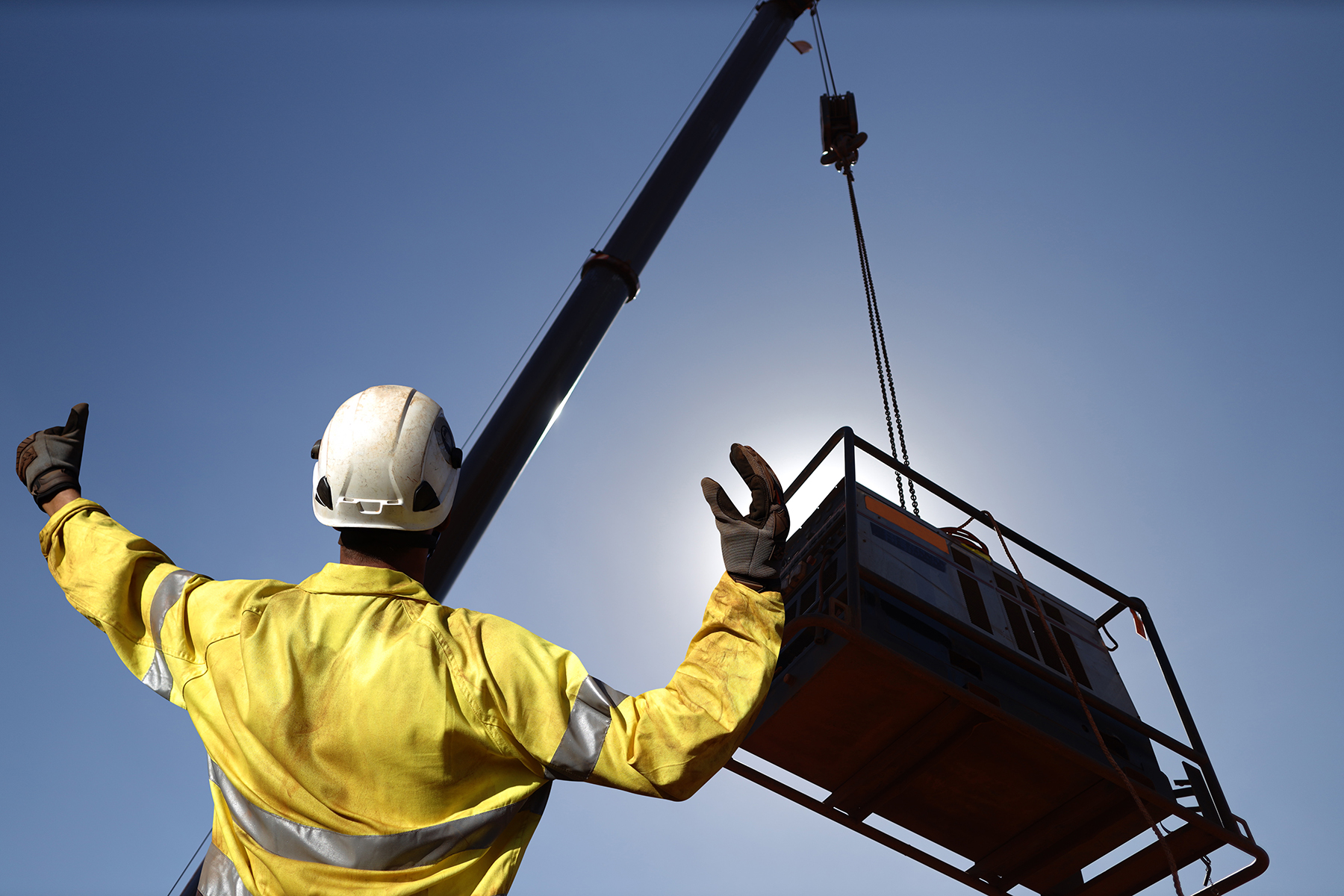
When it comes to rigging heavy machinery – often involving the movement of hundreds of thousands of pounds – safety isn’t just a priority, it’s the foundation behind every decision. The sheer weight and complexity inherent in industrial rigging services mean there’s no room for error.
The industrial contracting world is seeing rapid shifts and advances in technologies, and the realm of rigging safety is no exception. As the industry progresses into 2025, new technologies and methods are reshaping safety practices to ensure even the most complex lifts are conducted safely and securely.
IoT Devices: A Game-Changer for Real-Time Monitoring
The Internet of Things (IoT) is transforming industrial rigging services by embedding smart sensors into lifting equipment. These sensors provide real-time data on important safety factors like load stress, equipment health and environmental conditions. For example, operators can monitor the weight distribution during a lift, ensuring no single component is overburdened.
At Lee Industrial Contracting, our 75-ton calibrated load cell ensures precise load measurements, critical for safe and accurate lifts. This load cell undergoes monthly calibrations to guarantee its accuracy, providing operators with confidence that the equipment is performing at its best.
Additionally, our carry deck cranes are equipped with load moment indicators (LMI) that deliver exceptional precision with a tolerance of + or – 1% to 0.3%. These tools allow us to proactively monitor loads in real time and respond to any anomalies before they escalate into hazards.
IoT also enables remote monitoring so teams can immediately respond to issues before they escalate into hazards. This level of visibility eliminates guesswork, increasing both safety and efficiency.
VR and AR in Training and Onsite Precision
Virtual reality (VR) and augmented reality (AR) are providing safer, virtual environments in which to train and support rigging professionals. Through VR applications, workers can practice in realistic rigging simulations in a safe virtual environment without risk. Meanwhile, AR programs can display crucial information, like load limits or equipment positioning, directly onto a worker’s view during a lift.
VR and AR guidance helps minimize human error while fine-tuning precision in industrial rigging, especially for elaborate tasks in high-risk environments.
Advanced Equipment and Modeling
Safety innovations in industrial rigging services extend to the tools and techniques used on the ground. At Lee Industrial Contracting, we own and maintain state-of-the-art rigging equipment to ensure optimal performance and safety.
Our fleet includes ORMIG cranes, Tri-Lifters, Taylor Forklifts, Versa-Lift forklifts, gantries, and Goldhofer trailers, all of which are drawn and modeled in AutoCAD to develop precise rigging plans. This meticulous planning allows us to simulate each move in detail, identify potential hazards, and optimize every step of the operation before we set foot on-site.
Regulatory Evolution
In industrial contracting, industry regulations for safety are ever-evolving, and keeping up is paramount. These rules now require elements like certified equipment, detailed lift plans and continuous training for operators.
Companies offering industrial rigging services must stay ahead of these requirements by integrating new technologies and maintaining rigorous standards. For manufacturers and facility operators, partnering with an industrial contractor like Lee Contracting that adheres to these regulations ensures peace of mind and a safer work environment.
A Commitment to Innovation and Safety
Industrial rigging is a delicate balance between solving complex challenges while protecting people and assets. The innovations we’re seeing in 2025 will help up our game to create even safer environments.
In an industry where the stakes are high, investing in safety innovations isn’t just forward-thinking – it’s essential. By embracing cutting-edge technologies and practices, we’re not just lifting machinery, we’re lifting the standards for safe and efficient industrial rigging.
Have a rigging job ahead? Lee Contracting has the turnkey, in-house industrial rigging services that can help you complete the job quickly and safely. Contact us for a quote today.