Department: Safety and Foundations
Repurposing a vacant 40,000-square-foot industrial building, which had previously been used for manufacturing robotic weld cells, into a dynamic sports arena suitable for volleyball, badminton, cricket, and pickleball.
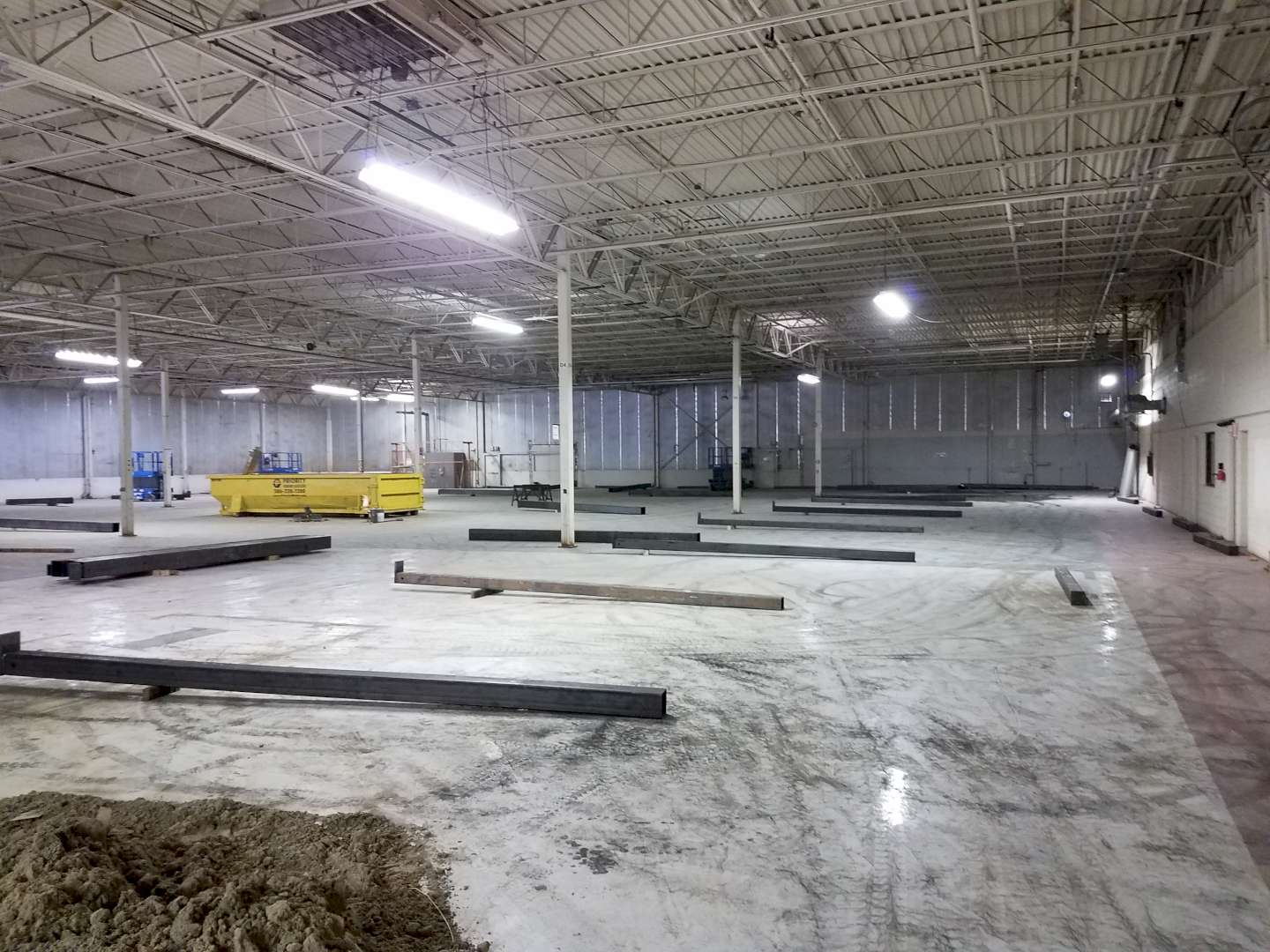
THE CHALLENGE
In the summer of 2020, as the world grappled with the onset of the COVID-19 pandemic, a group of entrepreneurs from Spare Holdings identified an opportunity to create a year-round, indoor sports facility in Novi, Michigan. Their vision was to repurpose a vacant 40,000-square-foot industrial building, which had previously been used for manufacturing robotic weld cells, into a dynamic sports arena suitable for volleyball, badminton, cricket, and pickleball.
The scope of the project included a substantial structural modification-raising a 160′ x 160′ section of the building’s roof by 10 feet. The project involved comprehensive design and construction efforts, encompassing electrical systems, steel structures, HVAC, plumbing, and general building modifications. The principal challenge was executing this intricate project with limited availability of supplies and significant vendor delivery delays. Ensuring safety, managing supply-chain disruptions, and maintaining project timelines under these constraints required careful planning and adaptability.
THE RESULTS
Following a successful planning and permitting phase, including collaboration with the city of Novi and Spare’s team, Lee Contracting initiated the physical transformation of the building in the winter of 2021. The project began with the demolition of existing walls and electrical setups to make room for the new sports courts. Despite facing extended lead times on key materials, such as building siding and rooftop HVAC units stretching from the usual four weeks to over six months Lee Contracting was able to easily navigate these challenges. The team was able to ensure a continuous flow of information and resources to keep the project on track and within budget.
A critical component of the construction was the manufacturing of new structural steel for the roof raise, which included the integration of larger girder beams necessary for the removal of two building columns. This phase culminated in a coordinated five-day process where the roof was elevated in one piece, facilitating the creation of expansive, unobstructed court spaces.
The project not only included structural enhancements but also the installation of new HVAC systems, the construction of modern offices, bathrooms, locker rooms, and a spectator mezzanine. Upon completion of the renovation, Spare awarded a 2nd phase to Lee Contracting that includes raising another 180′ x 80′ section of the building to help their operations meet the growth of their new business.
Subscribe and receive updates via email
Removal of 350,000 SF of trailer production equipment and installation of a new, fully automated production line.
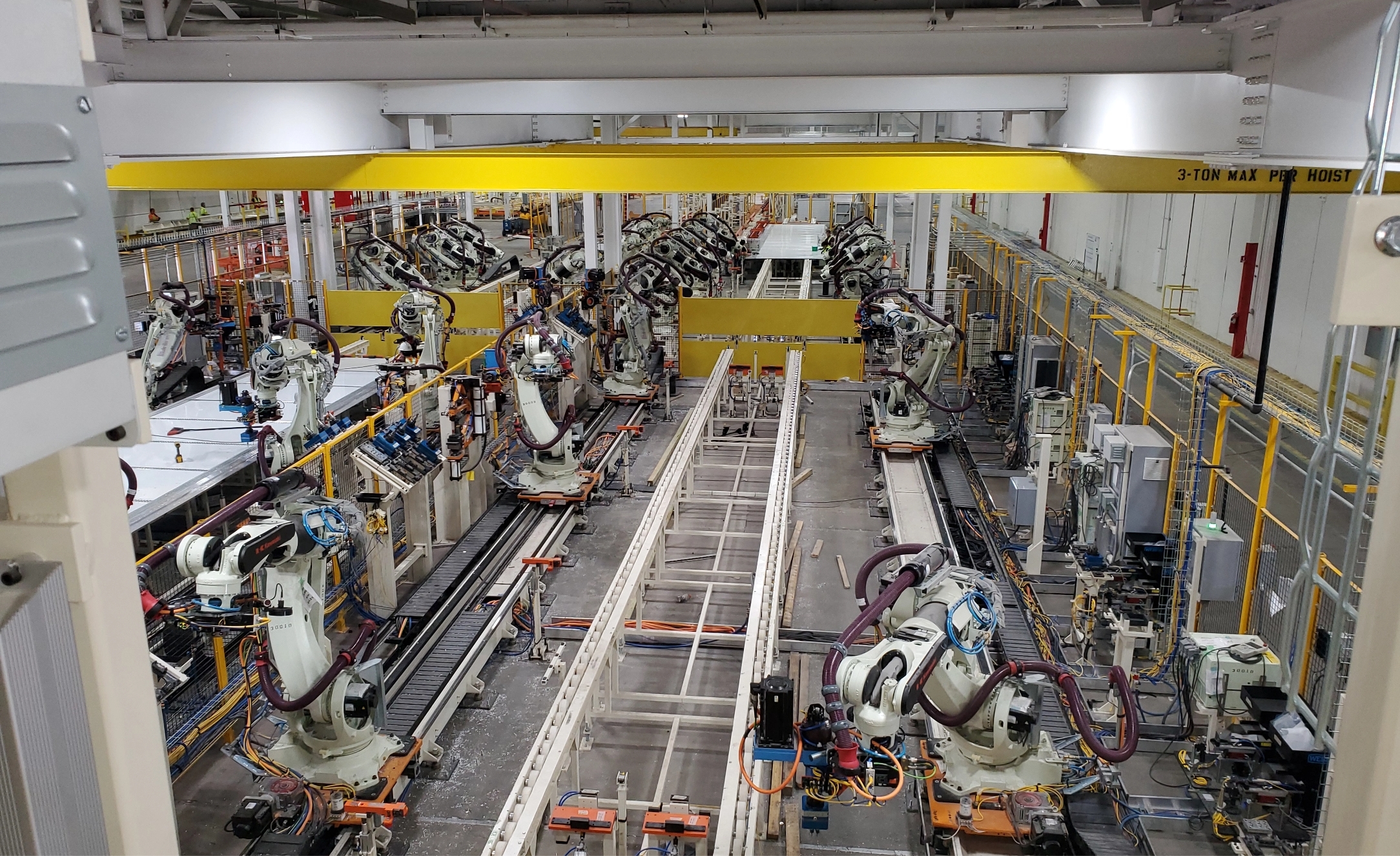
THE CHALLENGE
Wabash, a world-class manufacturer of advanced engineered solutions and services for the transportation, logistics and distribution industries, was searching for a contracting partner to remove 350,000 SF of trailer production equipment to make room for a new, fully automated production line. The project also included concrete flatwork removal and replacement with flat tolerances able to support automated guided vehicles (AGVs). As part of the job, Wabash needed the facility to be renovated, which included wall removal, truck dock installations, utility and structural steel modifications. Once the renovations were complete, Lee Contracting installed new automated equipment lines.
THE RESULTS
Lee Contracting worked very closely with the customer on the planning of this project. Resources were dispatched according to the plan which was an around-the-clock operation with over 100 people at the site. With our internal projects management, our trades people, and our safety team the project was completed safely and on time.
Lee Contracting worked closely with our concrete suppliers to make sure that there were no shortages for this project by securing orders early during the planning stages and the issue was flagged as a possible risk.