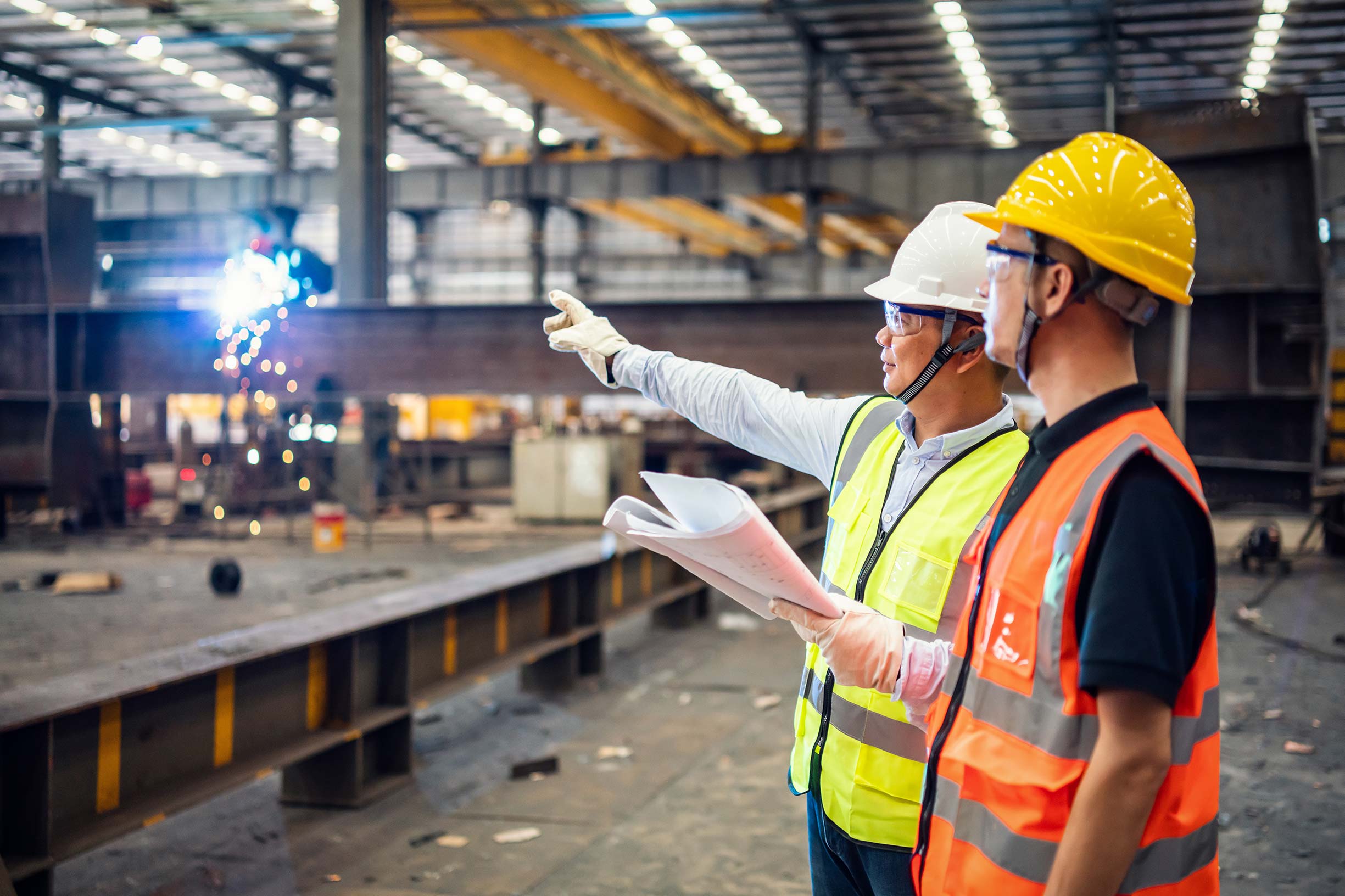
In light of the current manufacturing environment, a facility refresh may be the last thing on your mind. But even with supply chain problems, rising material costs, labor shortages and other pressures on your organization, finding opportunities for improving and maintaining your plant can help counter financial challenges.
Layout
If it’s been awhile since you considered the layout of your facility, it could be time for a revisit. Most any facility that’s been in operation for several years likely has opportunities for improvement, and even small changes to layout can have a big impact. You may have given a lot of thought to the horizontal dimension of your operations, but what about the vertical? Does your current layout take full advantage of the space above your production areas? Adding or modifying conveyors, platforms, catwalks or crossovers can help create a better workflow while improving productivity and safety.
Read More: Safety First in Industrial Contracting: Do’s and Don’ts From Safety Experts.
Gas Systems
With gas prices constantly fluctuating, you need to squeeze every ounce of energy out of your gas lines, and the last thing you need is an undetected leak. Start by matching the right type of detector with the application. From catalytic bead to ultrasonic units, find the type designed for the gases in your particular environment. If you don’t have them already, real-time gas detection systems produce immediate results and feedback, and are required in certain types of operations for protection of personnel and property.
Air Systems
Compressed air systems are a major factor in the cost of production, so ferreting out leaks should be top of your list for regular inspections. Systems should be checked around compressors, tanks and the entire air piping distribution. While difficult to see or hear, you may be amazed at the before and after results from a proper air pressure holding test and any required repairs. Depending on the shape of your current system, you could also be surprised at how quickly ROI is realized from this process.
Electrical Systems
Still lighting your facility with high pressure sodium or metal halide fixtures? If so, you may be missing significant savings in your overall energy costs. Switching your lighting to contemporary LED fixtures can greatly reduce energy costs while improving safety and your plant’s environmental impact. As a bonus for switching, there are many utility rebate programs available throughout the year that can offset your capital investment for this upgrade. Contact your energy supplier to find out if they offer any rebate programs.
HVAC Systems
Well functioning HVAC systems are critical for some manufacturing processes, such as food or pharmaceutical production. But regardless of what you make, a faulty system can be contributing to high energy costs that could be reduced. While you may be tempted to install new systems throughout the facility, a complete replacement may not be in the budget. Running system evaluations and ROI studies could indicate a better return on investment from replacing motor starters with variable speed drives. If your studies suggest a complete replacement with new, energy efficient systems, utility rebates should be researched to defray some of the cost of your project.
Water Systems
Water issues continue to elevate sourcing and discharge costs for industrial facilities. Do you have a water conservation strategy in place? Start by checking for leaks in equipment and piping systems, and set up a program to periodically check for opportunities to find and repair leaks. You should also be on the lookout for ways to minimize water use, such as installing monitoring devices or upgrading to equipment that more efficiently uses this valuable resource. Opportunities for reusing water should be examined thoroughly, as the practice can help reduce sourcing costs along with treatment and discharge costs.
Regular Maintenance
You might not think of your maintenance operations as part of a facility refresh. Reviewing and, if necessary, refining your maintenance program can help you discover opportunities for increased efficiency and reduced operating costs. Consider creating a predictive maintenance (PdM) plan which looks at numerous factors to avoid unplanned downtime and equipment failures while reducing unnecessary upkeep.
Read about our press maintenance and repair project.
Regardless of the scope of your refresh needs, the Lee team has the in-house experience and resources to deliver a turn-key product that will exceed your expectations. Our value engineering process and deep expertise help us produce the best and most cost efficient solution to any problem.
Considering a facility refresh? Let the experts at Lee find the ways to make your project more efficient and cost effective.