Metalworkers were valuable members of early societies. As more products and tools began to be made from metals, society needed more people skilled in the craft of metalworking. Objects made from metals are necessary for heavy industry, farming, jewelry-making and defense purposes. Precision metal stamping is now used in nearly every product we use. As the capabilities of the process improve, new markets are opened.
The evolution of coin making has led to the modern stamping press. Coin making developed into a process in which the coin was struck using two coining dies: a lower die depicting the coin in a negative form and a companion upper die. A metalworker placed a blank between these two dies and the upper die was struck with a heavy hammer, rendering a positive image on the blank. The hammer method was used well into the Middle Ages. Even today people occasionally speak of coins being “struck.”
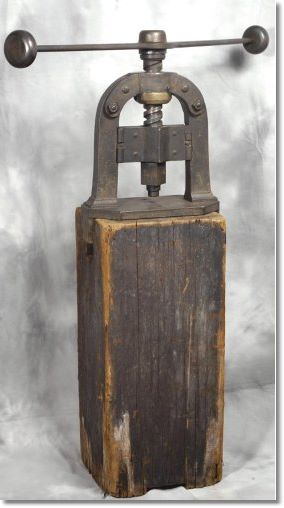
In 1550, a German silversmith, developed a screw press for stamping coins. The screw press was turned by as many as twelve men to exert the pressure needed to form the metal. As the industrial revolution approached, the brute force of the human powered screw press was replaced by using steam power to lift a heavy weight above the die and dropping it to strike the image. As technology improved, the speed with which coins could be stamped rose dramatically, but stamping metal parts for industrial use was almost unheard of until the 1890s. Prior to then, manufacturers relied on forging and die-casting for the fabrication of most metal components. However, in 1890, a German bicycle manufacturer began making parts for bicycles using metal stamping.
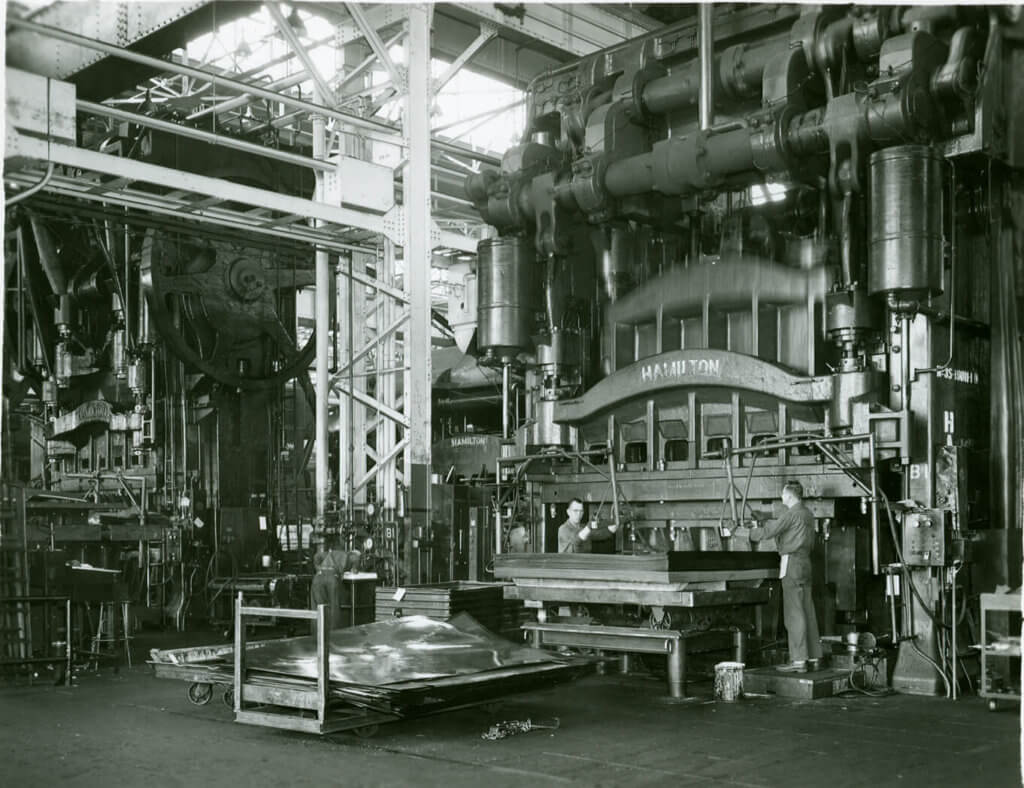
As manufacturers discovered how fast and inexpensive parts could be fabricated using metal stamping, the process began to flourish. Surprisingly, one of the last manufacturers to embrace the metal stamping of automobile parts was Henry Ford. An innovator in the assembly process, his engineers had to convince Ford that metal stamping for fenders and other parts was not only faster and less expensive than die-casting, but the quality was just as good. As production demands increased, Ford had no choice but to accept the new technology to keep up with demand.
Lee Contracting is ready to assist your next stamping press project whether you are relocating or installing. We can also perform all utility hookups to get your press running. We are your turnkey solutions provider delivering safe, cost efficient and reduced downtime projects.
Schedule your conversation with us by calling (888) 833-8776 or fill out our online form.